An Unbiased View of Alcast Company
An Unbiased View of Alcast Company
Blog Article
The Ultimate Guide To Alcast Company
Table of ContentsExcitement About Alcast Company9 Simple Techniques For Alcast CompanyThe Ultimate Guide To Alcast CompanyHow Alcast Company can Save You Time, Stress, and Money.Indicators on Alcast Company You Should KnowThings about Alcast CompanyAlcast Company for Beginners

If you think that a wrought alloy might be the most effective for your job, have a look at a few of our articles that explain more about specific functioned alloys, such as Alloy 6061 and Alloy 6063. On the various other hand, if you assume an actors alloy would certainly be much better for you, you can find out more regarding some cast alloys in our Alloy 380 and Alloy 383 write-ups (coming soon).
How Alcast Company can Save You Time, Stress, and Money.
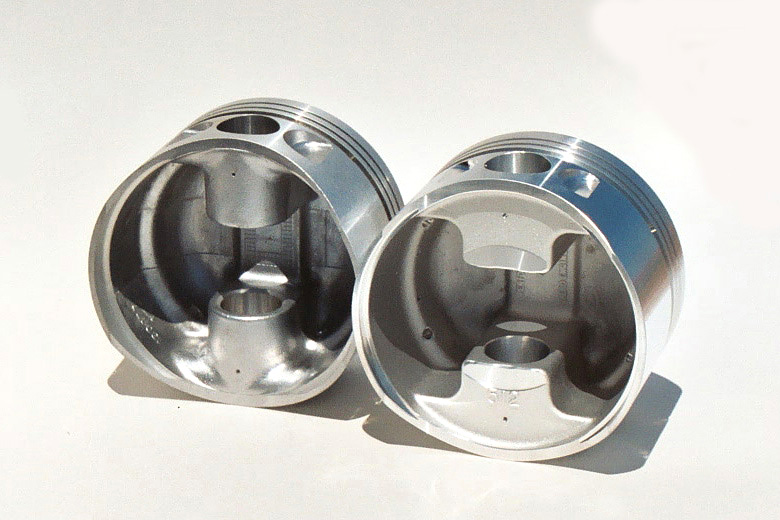
Having the experience and market expertise to engineer your spreadings for optimal manufacturing and quality end results will improve the job. Making aluminum spreading calls for a complex set of procedures to accomplish the appropriate outcomes. When choosing a brand-new aluminum foundry to partner with, ensure they have substantial sector experience and are knowledgeable regarding all elements of the light weight aluminum casting procedure: style, production, material analysis, and product screening.
(https://cfq0k7bjp5i.typeform.com/to/pc3E7Ixb?utm_source=xxxxx)The factory must also have a proven performance history of providing extraordinary items that fulfill or go beyond consumer expectations. Quality assurance needs to likewise go to the top of your list when choosing an aluminum shop. By functioning with a qualified factory who follows the criteria for high quality control, you can secure the honesty of your product and guarantee it satisfies your specifications.
What Does Alcast Company Mean?
By picking a business who provides services that fulfill or surpass your item demands, you can be certain that your task will certainly be finished with the utmost accuracy and performance. Specific aluminum foundries focus on specific sorts of making procedures or casting methods. Different components require different manufacturing methods to cast light weight aluminum, such as sand casting or die spreading.
Pass away casting is the name given to the procedure of developing complex steel elements with use of mold and mildews of the element, likewise understood as passes away. It produces more elements than any other process, with a high degree of precision and repeatability. There are three sub-processes that drop under the group of die casting: gravity pass away casting (or long-term mold spreading), low-pressure die spreading and high-pressure die spreading.
After the purity of the alloy is examined, passes away are developed. To prepare the dies for casting, it is important that the passes away are clean, so that no residue from previous productions stay.
The pure steel, likewise recognized as ingot, is included in the heater and maintained at the molten temperature level of the steel, which is then moved to the injection chamber and infused right into the die (Aluminum Castings). The pressure is after that kept as the steel solidifies. As soon as the steel strengthens, the cooling process begins
The Buzz on Alcast Company
The thicker the wall surface of the component, the longer the cooling time due to the amount of indoor steel that likewise needs to cool down. After the part is totally cooled, the die cuts in half open and an ejection system presses the part out. Adhering to the ejection, the die is closed for the next shot cycle.
The flash is the additional material that is cast throughout the procedure. This have to be cut off utilizing a trim device to leave simply the primary component. Deburring removes the smaller sized items, called burrs, after the trimming procedure. The element is brightened, or burnished, to give it a smooth coating.
Alcast Company Fundamentals Explained
Today, top makers make use of x-ray testing to see the entire interior of components without cutting right into them. To obtain to the finished product, there are 3 key alloys made use of as die casting material to pick from: zinc, aluminum and magnesium.
Zinc is one of the most secondhand alloys for die spreading because of its reduced price of resources. It's likewise one of the more powerful and secure metals. Plus, it has outstanding electric and thermal conductivity. Its deterioration resistance additionally enables the elements to be durable, and it is one of the much more castable alloys due to its lower melting factor.
Alcast Company - The Facts
As discussed, this alloy is one of one of the most frequently utilized, yet manufactures will, sometimes, select light weight aluminum over zinc because of aluminum's production advantages. Light weight aluminum is highly economical and among the more flexible alloys. Light weight aluminum is utilized for a variety of you can find out more different items and markets anything from home window structures to aerospace materials.
Report this page